Introduction
If you’re an industrial developer, I’m sure you’re already feeling the squeeze: construction costs are on the rise and fast. From spikes in steel to labor shortages in the skilled trades, budgets that once seemed solid are starting to buckle. No matter whether you’re looking to develop a warehouse, logistics park, or manufacturing unit, understanding the cost landscape is no longer an option; it’s a requirement.
Let’s unpack what is happening, what is causing it, and how intelligent developers like SVTN Group are responding appropriately.
Current Construction Cost Trends
The construction industry in India has experienced a consistent rise in input prices over the last five years, with industry data offering insight into the current state of the industry:
- Some areas have seen steel prices almost double since 2020.
- Cement prices have surged by around 20-30%.
- Labor wages have increased by 15-20% globally due to labor shortages along with rising inflation.
This is not just a momentary spike; these are new norms, and the projects that were feasible two years ago are being put under revisits and additional budgeting.
Must Read: Top Construction Companies in Pune
Key Factors Driving Rising Construction Costs
Multiple interrelated elements are driving the entire cost increase:
Materials Inflation: The inflation of core materials such as steel, cement, copper, aluminum, and many others has significantly increased and is affected by global supply chain issues and market & demand drives locally.
- Labor Shortages:
Various migration patterns after COVID have produced a shortage of available skilled and semi-skilled labor, and the cost of re-hiring and retraining is also higher.
- Land and Regulatory Costs
The price of land in industrial areas is increasing, along with compliance costs to environmental and safety standards.
- Transport and Fuel Costs
Fuel inflation impacts logistics, but moving materials, equipment, and labor to the site has all become significantly more expensive.
Impact of Rising Construction Costs on Industrial Projects
For developers, the ramifications are very real:
- Delayed project timelines as a result of cost reassessment
- Reduced ROI because budgets are higher than anticipated
- Cash flow pressure, especially for mid-size companies
- Difficulty attracting tenants or buyers if rents/prices increase to cover added costs
In short, rising costs can yield onboarding challenges as well as strategic considerations.
How Turnkey and Design-Build Models Help Control Rising Costs
Developers are responding by using turnkey and design-build delivery models. Here are some of the reasons:
- Single-point responsibility: one firm is responsible for both design and construction, which minimizes back-and-forth delays.
- Cost Predictability: With fixed-price contracts, there are fewer budget shocks.
- Faster execution: integrated into scheduling, timelines become tighter and are managed much better.
- Value engineering: The models allow the builder to present less expensive options to the end-user early in the design process.
In the case of industrial development, where time-to-market is paramount, this could mean the difference between profit and a missed opportunity.
SVTN Group’s Approach to Cost Management and Value Engineering
At SVTN Group, higher construction costs are not surprising; they are simply a hurdle to be dealt with.
They manage to be proactive in their approach by
- In-house engineering and design allow them to coordinate more effectively and identify cost threats earlier.
- Developed vendor relationships that give them leverage for better pricing or preferred supply even in material-shortage situations.
- Utilize modular and prefabricated parts so that on-site labor can be minimized and the duration of construction can be shortened.
- Incorporate programmatic value engineering into the design process to increase efficiencies with material usage and structural efficiencies.
By being proactive and not reactive, SVTN allows its clients to finish the project on budget, no matter how uncertain the market is.
Practical Tips for Developers to Mitigate Rising Construction Costs
When navigating your project, here are a few things you can implement to keep costs under control:
- Plan Early, Secure Prices
You should look to pre-order your steel, cement, and HVAC to eliminate the risk of a price surge in the future.
- Utilize Local Resources
Save on transportation costs by sourcing your materials and your labor from locations closer to your site.
- Leverage Technology
Sourcing project management software, drones, and BIM (Building Information Modeling) can produce vast efficiencies and reduce errors.
- Select the Appropriate Delivery Model
Consider turnkey or design-build to cultivate the most control and responsibility.
- Audit for Cost
Conduct monthly audits, not quarterly. Ships don’t sink from big holes; often, the first thing to go is small leaks.
Future Outlook and Trends in Construction Costs:
The outlook for construction costs isn’t looking good; an avalanche of cost drops isn’t in the forecast any time soon. Nevertheless, construction is changing:
- Green construction and energy-efficient building are on course to be the norm.
- Digital twins and automation of site operations will lessen reliance on labor.
- Precast and modular strategies will enhance efficiency in large industrial organizations.
For developers, remaining nimble and adaptive is going to keep you alive in upcoming challenges.
Conclusion
Certainly, construction costs are increasing, but there is a way to approach the new landscape of opportunities by building smarter. Commercial and industrial developers can provide quality, timely projects while being aware of what is changing and engaging models that provide control and clarity.
Examples and case studies, like the SVTN Group, demonstrate that although cost pressures do exist, value does not have to be compromised. Always at the center of smart design and development lies wonderful opportunity.
FAQ
Q1: How much have construction costs increased in the past 5 years?
In the past five years, construction input costs have risen on average 20-35%, depending on region and job type.
Q2: What are the biggest contributors to rising construction costs today?
The main drivers in that equation have been (or continue to be) raw material inflation, labor shortages, fuel costs, and regulatory compliance costs.
Q3: How does turnkey project delivery help control construction expenses?
Turnkey projects provide single-source responsibility, predictability of costs, and a faster time to finish, all of which help mitigate overall budgets.
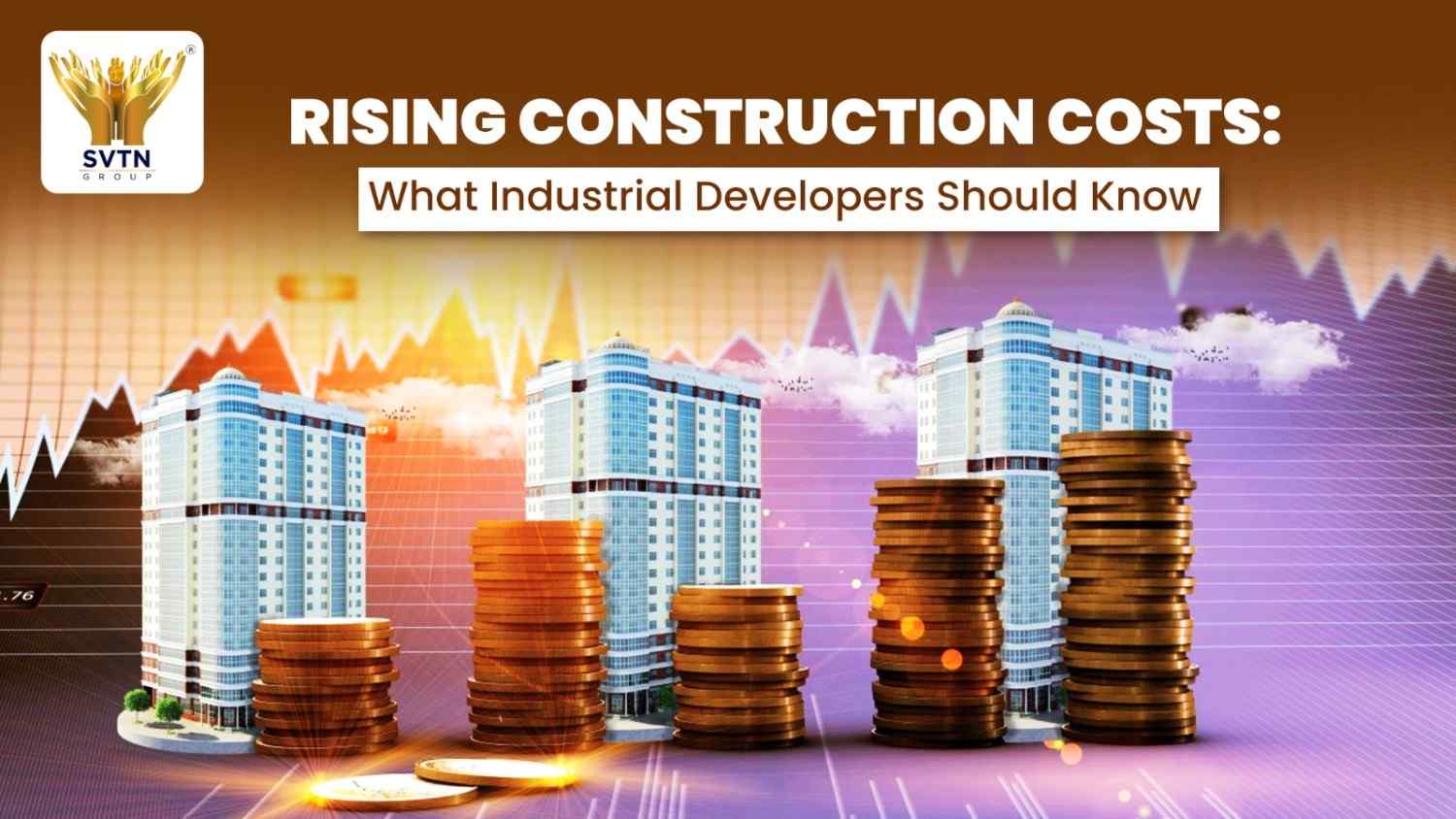
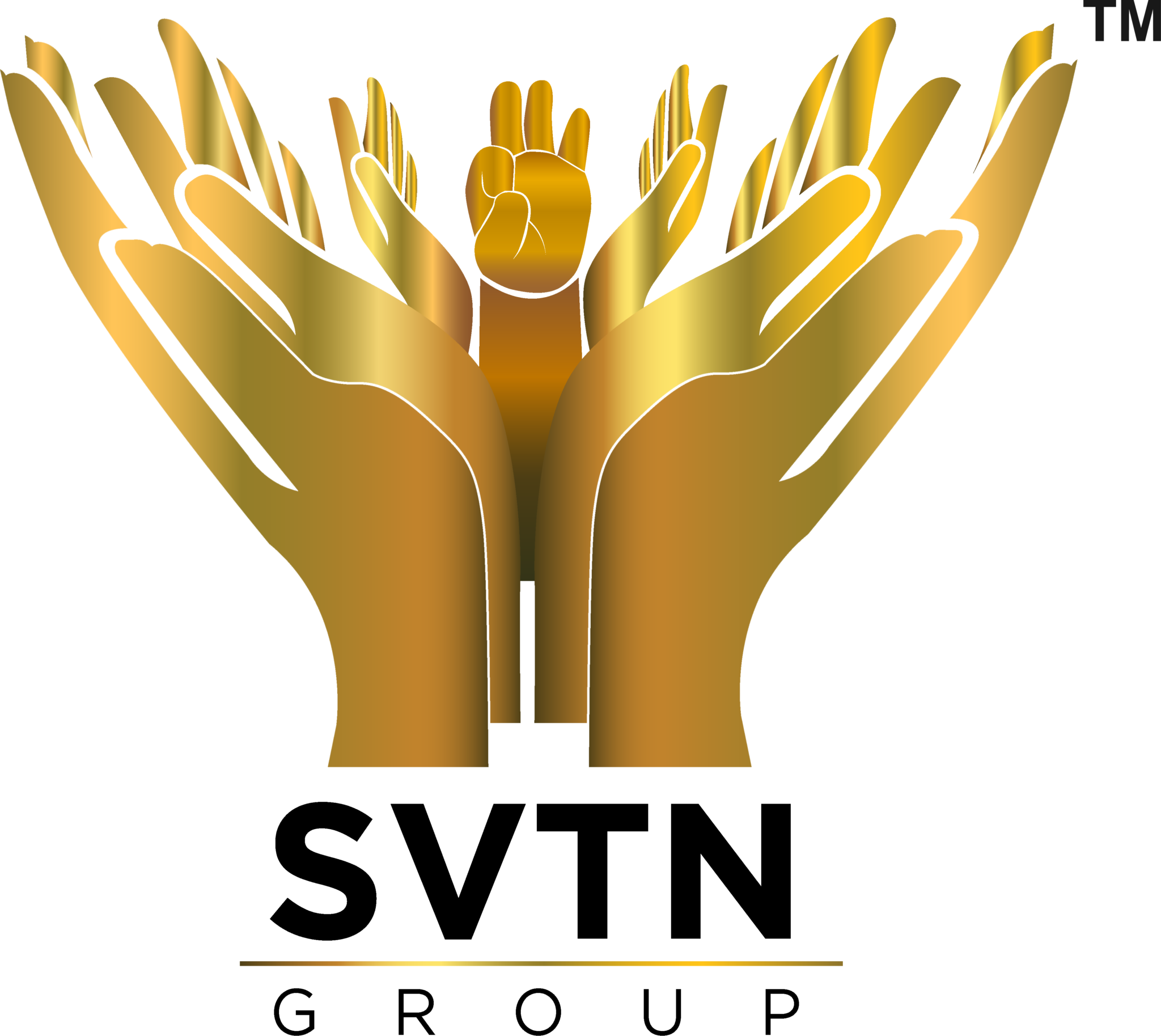